鋁鋅合金壓鑄的質(zhì)量控制貫穿于生產(chǎn)全流程,從原材料到成品輸出的每個(gè)環(huán)節(jié)都需嚴(yán)格把控,以減少缺陷(如氣孔、縮孔、裂紋、飛邊等),確保壓鑄件性能與精度。
?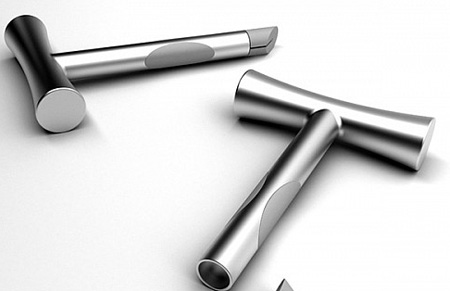
以下是關(guān)鍵質(zhì)量控制要點(diǎn):
一、原材料及預(yù)處理控制
合金成分管控
嚴(yán)格檢驗(yàn)鋁鋅合金錠的化學(xué)成分,確保鋅(Zn)、鋁(Al)及其他合金元素(如鎂、銅、硅等)含量符合標(biāo)準(zhǔn)(如 GB/T 1173 或客戶指定牌號(hào)要求),避免因成分偏差導(dǎo)致鑄件力學(xué)性能(強(qiáng)度、硬度)不達(dá)標(biāo)或流動(dòng)性下降。
禁止使用雜質(zhì)超標(biāo)的回爐料,回爐料比例需嚴(yán)格控制(通常不超過 30%-50%),并單獨(dú)檢測(cè)其成分穩(wěn)定性,防止雜質(zhì)累積影響鑄件質(zhì)量。
原材料預(yù)處理
合金錠需清潔無(wú)油污、銹蝕,投入熔爐前去除表面雜質(zhì),避免熔煉時(shí)產(chǎn)生氣體或夾渣。
潮濕的原材料需預(yù)先烘干(溫度約 120-150℃),減少熔煉過程中氫氣的吸入(氫氣是導(dǎo)致鑄件氣孔的主要原因之一)。
二、熔煉過程控制
熔煉溫度與時(shí)間
控制熔爐溫度在合金液相線以上 50-100℃(具體溫度依合金牌號(hào)而定,如 ZA27 合金約 450-500℃),溫度過高會(huì)導(dǎo)致合金氧化燒損加劇、晶粒粗大;溫度過低則流動(dòng)性不足,易產(chǎn)生澆不足、冷隔等缺陷。
熔煉時(shí)間不宜過長(zhǎng),避免合金元素過度燒損或吸氣量增加,同時(shí)需通過攪拌確保合金成分均勻。
除氣與精煉
熔煉時(shí)必須進(jìn)行除氣處理,常用方法包括:通入惰性氣體(如氮?dú)猓嚢?、添加除氣劑(如六氯乙烷),降低合金液中氫氣含量(氫含量需控制?0.15ml/100g 以下),減少鑄件氣孔。
加入精煉劑(如氯化鋅、氟化鹽)去除合金液中的氧化物、硫化物等夾渣,確保合金液純凈度,避免夾渣類缺陷。
熔體溫度穩(wěn)定性
合金液從熔爐轉(zhuǎn)移至壓鑄機(jī)壓室前,需保持溫度穩(wěn)定,避免因溫度波動(dòng)導(dǎo)致填充性能不一致,影響鑄件成型質(zhì)量。
三、壓鑄工藝參數(shù)控制
壓射參數(shù)
壓射速度:分為慢速(填充階段)和快速(增壓階段),需根據(jù)鑄件結(jié)構(gòu)(薄壁件需高速,厚壁件可適當(dāng)降低)調(diào)整,確保合金液快速充滿型腔且無(wú)飛濺、卷氣。
壓射壓力:包括比壓(單位面積壓力)和增壓壓力,需根據(jù)鑄件尺寸、壁厚及復(fù)雜程度設(shè)定(通常 50-150MPa),壓力不足易導(dǎo)致縮孔、欠鑄;壓力過高可能引發(fā)模具磨損或鑄件飛邊。
保壓時(shí)間與壓力:保壓階段需維持一定壓力至鑄件凝固,防止因金屬液收縮產(chǎn)生縮孔,保壓時(shí)間通常為 0.5-3 秒(隨鑄件厚度增加而延長(zhǎng))。
模具溫度控制
模具預(yù)熱溫度需匹配合金特性(通常 150-250℃),溫度過低會(huì)導(dǎo)致合金液快速冷卻,產(chǎn)生冷隔、澆不足;溫度過高則鑄件易粘模、表面粗糙,且冷卻時(shí)間延長(zhǎng)影響生產(chǎn)效率。
生產(chǎn)過程中通過模溫機(jī)實(shí)時(shí)監(jiān)控模具各區(qū)域溫度(如型腔、型芯),確保溫度均勻,避免局部過熱或過冷導(dǎo)致的鑄件變形。
澆注量與填充時(shí)間
控制每次壓射的合金液量(即 “料餅厚度”),確保填充型腔充分且無(wú)過量浪費(fèi),避免因澆注量不足導(dǎo)致欠鑄,或過量導(dǎo)致飛邊、漲模。
填充時(shí)間需極短(通常 0.05-0.5 秒),確保合金液在凝固前充滿型腔復(fù)雜結(jié)構(gòu)(如窄縫、薄壁處)。
四、模具設(shè)計(jì)與維護(hù)控制
模具結(jié)構(gòu)合理性
澆注系統(tǒng)(澆道、內(nèi)澆口)設(shè)計(jì)需確保合金液流動(dòng)平穩(wěn)、無(wú)渦流(減少卷氣),內(nèi)澆口位置與尺寸需匹配鑄件形狀,避免局部沖擊導(dǎo)致模具磨損或鑄件缺陷。
排氣系統(tǒng)需通暢,在型腔最后填充處設(shè)置排氣槽(深度 0.05-0.1mm),及時(shí)排出型腔內(nèi)的空氣和氣體,防止氣孔、欠鑄。
脫模斜度、頂出機(jī)構(gòu)設(shè)計(jì)需合理,避免鑄件頂出時(shí)產(chǎn)生變形或拉傷。
模具日常維護(hù)
定期檢查模具型腔、型芯的磨損情況,及時(shí)修復(fù)因沖刷、腐蝕導(dǎo)致的劃痕、凹陷,確保鑄件尺寸精度。
保持模具表面清潔,每次生產(chǎn)前噴涂均勻的脫模劑(避免過量導(dǎo)致鑄件表面缺陷),并檢查導(dǎo)柱、導(dǎo)套等運(yùn)動(dòng)部件的潤(rùn)滑,防止卡滯影響合模精度。
五、后處理及成品檢驗(yàn)
后處理質(zhì)量控制
去除鑄件飛邊、毛刺時(shí),避免因打磨過度導(dǎo)致尺寸超差或表面損傷。
如需進(jìn)行表面處理(如電鍍、噴漆),需先對(duì)鑄件進(jìn)行脫脂、酸洗,確保表面無(wú)油污、氧化層,避免鍍層結(jié)合不良。
對(duì)有內(nèi)部質(zhì)量要求的鑄件(如承壓件),需進(jìn)行時(shí)效處理(消除內(nèi)應(yīng)力),防止后續(xù)使用中變形或開裂。
成品檢驗(yàn)標(biāo)準(zhǔn)
外觀檢驗(yàn):通過目視或放大鏡檢查表面是否有氣孔、裂紋、縮坑、劃傷等缺陷,符合客戶外觀等級(jí)要求(如無(wú) A 級(jí)面缺陷)。
尺寸精度:使用卡尺、千分尺、三坐標(biāo)測(cè)量?jī)x等工具,檢測(cè)關(guān)鍵尺寸(如孔徑、壁厚、垂直度),確保在設(shè)計(jì)公差范圍內(nèi)(通常 IT10-IT12 級(jí))。
性能測(cè)試:抽樣進(jìn)行力學(xué)性能檢測(cè)(抗拉強(qiáng)度、硬度、延伸率),必要時(shí)通過金相分析檢查內(nèi)部組織(如晶粒大小、夾雜物含量)。
內(nèi)部質(zhì)量:對(duì)重要鑄件進(jìn)行無(wú)損檢測(cè)(如 X 光探傷、超聲檢測(cè)),排查內(nèi)部氣孔、縮孔等隱蔽缺陷。
六、過程記錄與追溯
建立完整的生產(chǎn)記錄體系,記錄每批次的合金成分、熔煉參數(shù)、壓鑄工藝參數(shù)(溫度、壓力、時(shí)間)、模具狀態(tài)、檢驗(yàn)結(jié)果等,確保質(zhì)量問題可追溯,便于分析缺陷原因并優(yōu)化工藝。